SITUATION
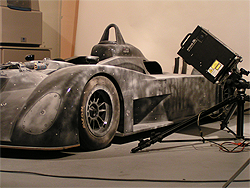
Scanning the racer DP02
A standard fiberglass lay-up process is used to create the shell (outer body mold) of the VanDiemen DP02 Sports Racer. Based off the model design of an existing racer body, the client needed to know the shell’s dimensions to correctly place the engine and chassis. The DP02 also required optimization of packing density and weight ratios to maximize the performance of the car. Due to the complex and free form surfaces of the shell, as well as the critical aerodynamic features, they would need to use 3D scanning technology to ensure that the dimensions were measured as accurately as possible.
SOLUTION
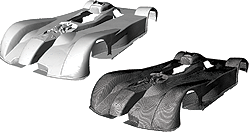
CAD data for the racer
Our team was contracted to perform 3D laser scanning and reverse engineering services on the DP02 shell. The client transported the racer to our Engineering Service Center, where it was scanned using the Konica Minolta VIVID 9i. Our team used photogrammetry in conjunction with the VIVID 9i to ensure the scan data captured was within a tight 0.002 inch tolerance.
Our engineers used the scan data acquired by the VIVID 9i to reverse engineer the car. Working with Rapidform’s powerful reverse engineering software, our team generated accurate IGES surfaces of the racer. Rapidform enabled us to maintain a high level of control over the surface network of the car, ensuring that the CAD data was as accurate as possible for testing and optimization purposes.
RESULTS
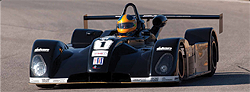
DP02 Sports Racer
The CAD data supplied by our team was a success for this client’s digital optimization of the DP02 racer. Using this data, they were able to lower the weight of the car while increasing performance, ensuring the future success and competitive advantage of the VanDiemen DP02 Sports Racer. Our team’s ability to deliver exactly what the client needed paved the way for many future projects with this client and their partner company.